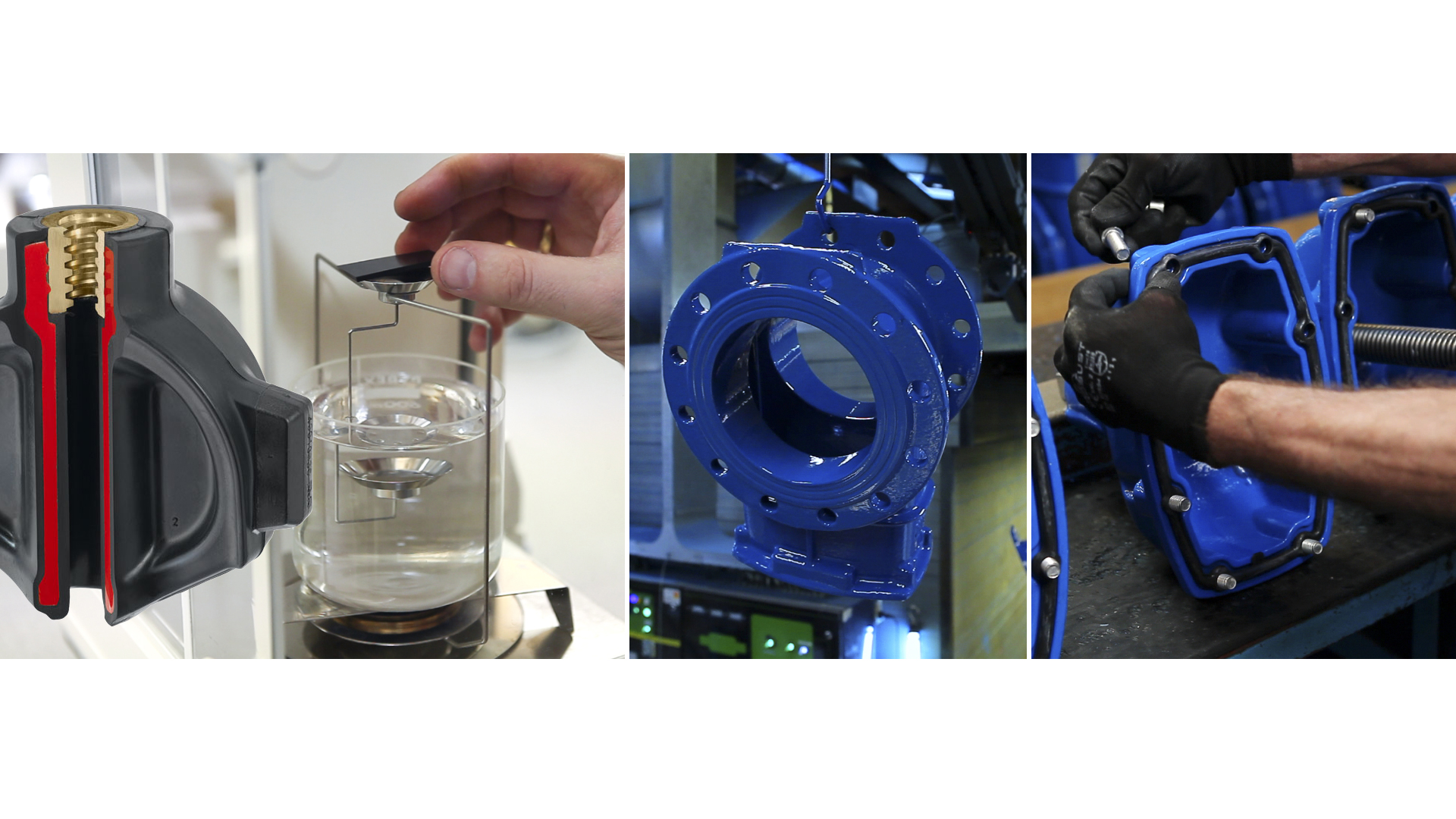
How to choose the right gate valve
To avoid costly replacements, it’s essential to choose a gate valve with a strong, durable design. There are five key factors to consider for making the best selection.
1) The ideal wedge design
As the sealing component of a gate valve, the wedge is a critical factor. Consider these points:Different types of wedge nut designs
The wedge nut connects the wedge to the stem and there are two main designs; A loose wedge nut, where the brass nut moves in a slot within the wedge core, and a fixed wedge nut, where the nut is expanded into the wedge core. A fixed wedge nut reduces the number of movable parts, minimizing the risk of corrosion caused by the movement wearing down the rubber surface of the wedge core. A fixed wedge nut design is therefore recommended.Wedge guides and shoes
During valve operation, the wedge experiences friction and stress as it moves. Guides, which fit into grooves in the body, help keep the wedge stable and prevent the stem from bending due to the flow. Wedge shoes protect the rubber on the wedge surface from wearing out due to friction. Make sure the shoes are properly fixed to the wedge and that enough rubber is present beneath to protect against corrosion.Rubber
The valve’s tight seal depends on the wedge being fully vulcanized with rubber. The rubber must be thick enough on the sealing surface to absorb impurities. It’s also important that the rubber bonds strongly with the wedge core, ensuring proper sealing even under compression and preventing corrosion caused by penetrating sharp objects when the valve closes.2) Rubber quality – compression set, durability and approvals
Rubber quality plays a vital role in the valve's longevity and performance. The rubber must withstand continuous contact with impurities and chemicals, and it must effectively absorb small particles in the seat to ensure tight closure. Key points to consider:Compression set – retaining original shape
Compression set refers to the rubber’s ability to return to its original shape after having been compressed. The EN 681-1 standard states the minimum requirements for the compression set value, but the better the compression set, the more effectively the rubber will maintain a tight seal over time.Preventing biofilm formation
Organic substances migrate from the rubber compound and act as nutrients for microorganisms, which will then start forming biofilm causing contamination of the drinking water. Select valves with a wedge rubber that ensures minimum formation of biofilm.Resistance to water treatment chemicals
Rubber must resist degradation from chemicals like chlorine or ozone, which are often used to clean pipelines. If the rubber cracks due to chemical exposure, the wedge core could corrode.Drinking water approval
Rubber components in contact with drinking water should meet recognized drinking water standards, such as DVGW/KTW, KIWA, or NF, ensuring safe use in water systems.3) External corrosion protection
The external corrosion protection is critical for the service life of the valve. A uniform and even epoxy coating in compliance with DIN 3476 part 1, EN 14901 and GSK* requirements is recommended and involves the following:
- Blast cleaning following ISO 12944-4.
- Coating thickness of at least 250 μm on all areas
- MIBK test, to check curing and ensure no matt or smeared surface.
- Impact resistance test by dropping a steel cylinder onto the surface and ensuring no electrical breakthrough.
- Freedom of pores tested e.g. by means of a 3kV detector with a brush electrode used to reveal and locate pinholes in the coating
4) Tight construction
There are two important design issues:Stem sealing
The sealing placed in the bonnet around the stem should be maintenance-free and should last the service life of the valve or at least fulfil the service life demands according to EN 1074-2. Ideally, it should be a hydraulic seal, tightening as internal pressure increases, with backup seals. To prevent contamination, a top seal should also be used. High-quality EPDM rubber is necessary where the valve comes into contact with drinking water.Bonnet/body sealing
The seal between the bonnet and body should use a gasket secured in a recess, ensuring it stays in place and doesn’t blow out during pressure surges. To protect the bonnet bolts against corrosion the bonnet gasket should encircle the bolts, and the bolts should be embedded in the valve in such a way that no threads are exposed to the surroundings.5) General performance
Whether operated by handwheel or actuator, it's important to consider both operating and closing torque.Operating torques
The force needed to move the valve from open to closed should range from 5 Nm to 30 Nm, depending on size. If the operating torque is too low, the valve may be closed too quickly, leading to pressure surges or water hammer.Closing torques
The torque needed to close the valve to a drop tight position. This torque should for handwheel operated valves be balanced against the handwheel diameter in such a way that it does not present the operator with a rim-force in excess of 30-40 kg. When operating the valve with an electric actuator or manual gearbox the torque should be within the limits of a standard range actuator. It is important to notice that the actuators normally have a torque range that is quite wide, and often it is the ISO flange connection between valve and actuator that determines the actuator choice. As a main rule valves with ISO flange connection should have max. closing torques as stated below:
- ISO flange F-10, maximum 120 Nm
- ISO flange F-14, maximum 500 Nm
- ISO flange F-16, maximum 1000 Nm
Full bore
To enable the use of pipe cleaning devices the inside diameter of the valves should correspond to the nominal size of the valve.
*GSK stands for Gütegemeinshaft Schwerer Korrosionsschutz, and is an independent quality association with about 30 members, all leading European valve and fittings manufacturers. GSK outlines requirements for the coating itself and for the control procedures of the finished coating.